全国首座全方位装配式地铁站在青岛地铁6号线可洛石站拼装完成
2.3万吨重“超级积木”搭起来啦!
◆安装精度控制在2毫米以内 ◆获18项专利技术 ◆节省工期4-6个月
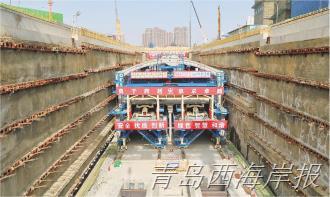
装配式车站拼装现场。
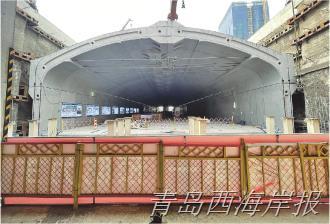
青岛地铁6号线可洛石站。
□本报记者 董梅雪
512块预制构件在工厂生产后运送到施工现场,在挖好的基坑内通过“搭积木”的方式进行拼装,最终建成一座深近23米、宽约25米、长220米的地铁车站……4月27日上午,随着最后一颗螺栓紧固完成,全国首座全方位装配式地铁车站——青岛地铁6号线可洛石站主体结构拼装顺利完成。
青岛地铁6号线整体位于西海岸新区,一期线路全长30.8公里,全部为地下线路,共设车站21座,可洛石站、黄海学院站、朝阳路站、富春江路站、淮河西路站、河洛埠站等6座车站为装配式车站。其中,可洛石站为地下两层标准车站,30多名工作人员用时6个月,最终完成了拼装总重达2.3万吨的全国首座全方位装配式地铁车站。
当天上午,记者来到可洛石站施工现场,探访“超级积木”搭建背后的奥秘。
科技创新>>
攻关解难题,获18项专利技术
“装配式地铁车站是一种新型的装配式建筑,就是把车站构件在预制厂内集中生产,然后在施工现场像‘搭积木’一样将预制构件一块一块按顺序拼装成型。”在青岛地铁六号线有限公司总工程师黄成的带领下,记者下入深近20米的地铁站。
远远望去,车站通过弧形的边墙和吊顶相连,形状犹如隧道,与传统现浇工艺建造的车站并无不同;走近时便可发现,车站的墙、梁、板、柱都是由一块块石板组合而成。早在去年,记者就曾到过可洛石站施工现场,那些超大体积、超大重量的车站预制构件给记者留下了深刻的印象,最重的底板构件长度超过20米,重达113吨。自去年10月底开始,30多名现场作业工人便在此搭建这些“巨型积木”,整座车站预制构件加起来共2.3万吨,实现了梁、板、柱、墙100%装配。
为确保地铁结构质量,装配式车站对构件的预制、拼装的精度要求极高,这就要求“积木”既要做得好,又要拼得准。
“早在工程设计阶段,青岛地铁六号线公司就牵头组织成立了专项科研攻关小组,邀请多位中国工程院院士及业内权威专家论证指导,全面进行技术创新优化,克服了地铁施工场地小、地下结构防水要求高、车站顶部荷载大等困难,形成了整套施工技术标准,为后续车站预制拼装奠定坚实基础。”黄成说道。
记者获悉,青岛地铁六号线公司还为装配式车站“量身定制”了施工装备,自主研发了具备旋转、精确自动定位、防摇摆、姿态微调、纠偏等多项智能化功能的“160吨智能龙门吊+整体分离式台车”等全套工装设备,解决了大型构件预制、翻转、吊装等难题,有效保证了构件拼装精度及大型构件的吊装安全。
截至目前,通过技术研发攻关,6号线共取得各类装配式车站施工专利技术18项,形成了整套的、具有自主知识产权的全方位装配式车站预制、拼装技术。
提质增效>>
全预制装配,施工时间减七成
在传统建筑施工现场,通常要有木工、钢筋工等各类小工种,而装配式建筑施工现场则更为简单,基本上只有装配工人一个工种。原先搭建一层楼房大约需要四五十人,现在十几个人就能完成,节约了大量人力。
而通过应用装配式施工,工期就能大幅缩减。黄成告诉记者,与传统工艺相比,全方位装配式地铁车站的各类构件均在专门的预制厂内生产加工,不受施工现场场地、气候、材料等条件的限制,可在基坑开挖阶段同步进行预制生产。
“在现场具备拼装条件后,通过智能门式起重机起吊拼装,工人只需引导和连接好各‘积木’就位即可,不再需要传统的‘支模打灰、覆盖养护’,安全风险有效降低,实现了装配现场作业时间减少约70%,施工人员数量减少80%,节省工期4-6个月。”黄成说。
地铁车站全预制装配是一种全新的施工工艺,需要大量的技术创新来支撑。在地铁6号线的装配式车站建设中,6号线创新了多项施工工艺。“我们创新设计了预制构件流水作业生产、蒸汽养护流程,使预制构件通过自动化流水作业、辊道运输的方式,采用模具随动、工位固定、油缸顶进传动技术,使大型预制构件厂区设计、物流动线、流水生产线规划布局合理,实现了构件预制的自动化、信息化、智能化生产。”
此外,在施工图设计、方案研究、场地规划等方面广泛应用BIM正向设计、三维建模等技术手段。如利用BIM三维模拟碰撞演示装配施工全过程,提前发现解决存在问题,并通过工序模拟动画让现场技术人员和作业工人更直观地了解施工技术要点,提升技术交底质量,确保将施工安装精度控制在2毫米以内。
低碳建造>>
碳排放降20%,建一流绿色地铁
用“搭积木”方式建起来的车站,质量能过关吗?许多头一次听说装配式建筑的市民不免有这样的疑虑。
对此,青岛市住房和城乡建设局市政公用监督站轨道二科科长高永冬说:“前期,我们组织人员到国内有相关经验的城市调研,并制定了装配式施工的相关标准。此外,地铁6号线是按照示范工程的标准来打造的,开建初期,便搭建了智慧工地平台,加强质量安全管理。目前,整个6号线的施工质量是合格可控的。”
与传统现浇车站施工方法相比,一座标准全方位装配式车站可减少用工80%,节省钢材约800吨、木材约800方,建筑垃圾减少60%,碳排放降低20%。施工现场不再使用脚手架等周转材料,有助于施工现场告别“脏乱差”的传统形象。
青岛地铁6号线深入践行绿色发展理念,成立专项课题研究团队,开展预制化、装配化研究,全面推广预制装配技术在地铁施工领域的应用。自开工建设以来,先后在围挡、便道等十余个方面采用预制装配工艺,为6号线服务的装配式生产企业达17家,预计产值达13亿元。全方位装配式车站技术在地铁6号线的成功应用,是青岛地铁深入践行国家“双碳”战略的体现,是落实青岛地铁“建成世界一流绿色地铁,实现节电30%、降碳40%”目标的重要举措,将有力推动地铁工程建造技术绿色转型发展。
记者还了解到,日前,青岛地铁6号线朝峨区间左线小里程段盾构机在朝阳路站正式始发,标志6号线土建05工区8台盾构全面进入掘进阶段。截至目前,6号线一期工程全线车站主体土石方开挖全部完成,5座车站封顶,7个单线区间贯通。一期工程累计始发盾构/TBM设备34台次,机械区间掘进累计完成45%。